By: Ko Ihara and Kashif Javed
Cornell ECE476, Spring 2006
WARNING: Solderpaste is highly toxic and 115/230 VAC is very dangerous!
Prevent any skin contact with solderpaste and never place food inside a reflow oven.
Take measures to prevent risks of lethal electrocution.
Our project consists of making a reflow soldering device using a normal toaster oven with a graphical LCD display for control and GUI. Soldering is an important and difficult task for custom printed circuit board design especially for integrated circuits that come as chip packages that are impossible to solder by hand. This is particularly true for ball grid arrays (BGA) and small-pitch quad flat packs. If one chooses to design a custom printed circuit board around these chips, then the designer may wish to also purchase a stencil of the designed board that would allow him to squeegee solderpaste precisely on the SMD pads. The designer would then carefully place the components on the board, and heat the solderpaste with a heat gun or a reflow soldering oven. The problem with soldering ovens is that they are expensive and cost thousands of dollars. We have decided to come up with a cheap and working solution to the problem by using a normal toaster oven and controlling it through a microcontroller along with an LCD display that guides the user through the soldering process and constantly provides feedback on the state of the system while reflow soldering. The input to the system would be via a conventional keypad and would consist of target temperature point at specific times that the user would enter based on the solderpaste's recommended tempearture profile. The system would interpolate the temperatures for the in-between time intervals and follow the curve generated by the input. The system would also fulfill the appropriate safety requirements and have the capability of aborting the process in case of a mishap.
Rationale and source:
The source of the project was one of the team members Ko Ihara who as part of his M.Eng. project worked on designing a circuit board and came up with the idea of using a toaster
oven for reflow soldering. The project idea fully complies with the requirements of the course and the challenging part is coming up with a workable PID feedback control to make
the toaster oven follow the temperature curve and heat up or cool down at appropriate times. The Atmel mega32 chip is sufficient for this project as the speed of the chip and
the number of I/O pins suffices our needs. Another thing about the project is that it would benefit future students in the course since they would be able to solder boards with
less pain and high efficiency and safety.
Logical structure:
The project can be divided into three parts namely the LCD display, the oven control and lastly the temperature sensor inside the oven.
The following block diagram shows the logical structure of the system.
The microcontroller sends a digital signal to the solid state relay switch which controls the on/off state of the oven for appropriate heating and cooling.
The temperature sensor device inside the oven makes a voltage divider circuit in series with a resistor, the voltage signal is connected to the atmel mega32
ADC (analog to digital converter) input. The ADC output is used as a feedback by the program to measure temperature inside the oven and to control the relay
state. At the same time, the state of the system is updated in real time on the LCD and the user can see the progress. The keypad is used for input and the
LCD provides step by step instructions to the user during the input process. The oven control hardware containing the relay switch is inside a metal box
with the fuse circuit in place. It has the three pin plug connections for connecting the oven and the AC voltage supply. It also has harness plugs for
connecting the digital input to the microcontroller.
Hardware/Software tradeoffs:
The LCD RAM was emulated in software through a buffer as it was not possible to read it in real time from the RAM.
Relationship with Standards:
In the United States, the alternative-current electric power transmission was standardized by Westinghouse in the 1890s and the 115/230 VAC standard for
home appliance was adopted since the early 1900s. We could not find an IEEE standard that is specifically relevant to the power distribution method. As
for the FCC regulation, our project has nothing to do with that.
Trademarks and Patents:
There are several patents associated with the design of a solder reflow oven, such as U.S. patent 6794616 by Lakhi Nandlal Goenka in 2004.
However, these are IPs are specific to the detailed design of the oven, not the general concept of reflow soldering itself.
There are several companies like Harotec/ SAB and Novastar that make reflow ovens but these are expensive devices targeting high-end commercial
markets where as our project is intended towards hobbyists and students who can not afford these products.
HARDWARE:
MCU:
The microcontroller that we used is an Atmel MEGA32 chip. It was soldered on the custom prototype board provided for this course.
We are using all the four ports A-D for I/O and therefore all of those were soldered on the board. The MCU is programmed via the STK 500 board.
LCD and Keypad:
The keypad used is the same as for previous labs. It is connected to PORT C
and is debounced to nullify the vibrating effect of the buttons due to their
mechanical nature. The LCD used for the project is a 128 x 64 pixel graphical
display model manufactured by Crystalfontz America, Inc. It has a 20 pin interface
with a 5.0 V requirement for logic and 8.0 V requirement for the LCD display.
The LCD is soldered on a prototype board along with the keypad. It is connected
to PORT B and PORT D (6 pins out of 8) of the mcu. Both ports are used as output
providing the necessary signals to the LCD for the control. The LCD has a KS0108B
controller built in it and is divided into two columns of 64 x 64 pixels with
a column select pin to switch between them. Each column is further divided into
8 pages with each page consisting of 8 rows of 64 pixels each. The LCD RAM that
corresponds to 128 x 64 pixels or 1K bytes is addressed in a way that all 8
rows belonging to the same column (y axis, not to be confused with the two columns
mentioned above) in a page can be read or written at a time. The pixels are
set on high logic and cleared on low. The set p and hold times for addresses
or data were of the order of nanosecond which means that the LCD interaction
could be easily done in real time. The LCD was powered through a voltage divider
circuit using the Maxim ICL7660CPA reverse voltage generator which is also soldered
on the prototype board.
Relay Box:
The relay switch used for the project was sampled from Omron Electronics and has the maximum rating of 75 A at 24 to 240 AC which is more than enough for a normal toaster oven.
The relay switch was placed in a heat sink metal box with three input plug connectors mounted inside to connect the toaster oven and the AC power supply.
The digital input was connected via harness plugs that were drilled into the box. The signal for the solid state relay switch was given through PORTD5 via the prototype board.
Thermistor:
The temperature device used was an NTC thermistor with temperature range from -40 to 300 Celsius. The device was placed inside the oven and connected to the voltage divider
circuit on the prototype board. The thermistor was connected in series with a 2K ohm resistor and was powered through an LM711 op amp which acted as a buffer or voltage
forwarding device. The variable voltage output from the circuit is fed to the mega32 via pin A0 that goes into the ADC on the chip.
The system is fairly easy to replicate, however care must be taken when connecting the various signals especially the relay box as it requires dealing with live 240 AC supply and must be done by trained personnel.
Pleases refer to appendix B and the pictures for an illustration of our hardware design. For further assistance, refer to the data sheets of the various components in appendix E.
Port | Function |
PORTA0 | Thermistor voltage |
Port | Function |
PORTB0 | DB0 (LCD) |
PORTB1 | DB1 (LCD) |
PORTB2 | DB2 (LCD) |
PORTB3 | DB3 (LCD) |
PORTB4 | DB4 (LCD) |
PORTB5 | DB5 (LCD) |
PORTB6 | DB6 (LCD) |
PORTB7 | DB7 (LCD) |
Port | Function |
PORTC0 | Pin 1 (Keypad) |
PORTC1 | Pin 2 (Keypad) |
PORTC2 | Pin 3 (Keypad) |
PORTC3 | Pin 4 (Keypad) |
PORTC4 | Pin 5 (Keypad) |
PORTC5 | Pin 6 (Keypad) |
PORTC6 | Pin 7 (Keypad) |
PORTC7 | Pin 8 (Keypad) |
Port | Function |
PORTD0 | CS1 (LCD) |
PORTD1 | CS2 (LCD) |
PORTD2 | Reset (LCD) |
PORTD3 | R/~W (LCD) |
PORTD4 | D/~I (LCD) |
PORTD5 | Relay signal |
PORTD7 | Enable (LCD) |
Speed:
The system worked at our desired speed. The LCD display worked in real time without any noticeable delays. The relay triggering was fast. Since the system was updated every second, the latency of the key scanner and the PID control was hidden because mega32 at 16MHz frequency was able to perform all the instructions without missing any interrupts.
Accuracy:
Given the experimental conditions and the hardware we had, the accuracy was good enough. The system was able to follow the target curve within a 10 degree Celsius locus. We tested the system by putting solder inside the oven and were able to melt the solder in a 210-240 degree Celsius range.
Safety:
Proper care was taken in building the system. The relay switch was place inside a heat sink metal box to ensure heat dissipation. Thermal paste was layered between the box and the relay. The box contains a fuse holder to regulate the current provided to the system. All the connector plugs were inserted on plastic insulated washers avoid short circuiting. The relay box was tested in the presence of Professor Land before plugging to the toaster.
Interference:
The system did not interfere with any other project and no complaints were made against the system by any group.
Usability:
The LCD display makes our system highly interactive and easy to use. The keypad was debounced to ensure correct input and appropriate error messages were displayed on erroneous input.
Analysis:
We are happy with the performance of our system. One of the problems we faced was cooling the system i.e. if the future target points show a decrease in temperature at a steep gradient, then the actual curve would be slightly off. This is due to the inertia of the oven. The heating coil retains the heat for a while even though the oven is off. This causes a slower decay in temperature. Similarly, a steep rise in temperature is also not readily achievable due to the heating limitation of the toaster oven.
One of our future advancement would be to add a cooling system to the project. We can add fans that are triggered if the current temperature is higher then the target temperature. Another idea is to use a fan to blow hot air in the oven instead of using the heating coil. This way the same blower can be used to heat and cool the system by changing the temperature of the air blown in.
The toaster oven used was an old one and had an inaccurate temperature controller inside which caused it to shutdown sometime even though the temperature was below the specification on the oven. This hindered our project a little particularly in heating up the oven. But this can be resolved by using a better quality oven.
Intellectual property considerations:
We re-used the video_line code from lab4 and a sample code for the LCD was used as reference for our LCD functionality. No reverse-engineering was done and neither did we have to sign an NDC form for sampling any of our parts. Our design is simple and the product we present is cheaper then its rivals in the market, therefore there could be patent opportunity for our product.
Ethical considerations:
We believe that our project conforms to the ethical considerations and is consistent with the IEEE code of ethics as explained below.
toaster.c
#include <Mega32.h>
#include <delay.h>
#include <stdio.h>
#include <math.h>
#include <stdlib.h>
#include <string.h> #define begin {
#define end }
#define map_size 128*64/8
#define max_time 340
#define base_temp 0
#define room_temp 40
//Timing
#define t1 30
#define t2 1000
//Keypads
#define maxkeys 13 //characters
#define no 11
#define yes 12
#define quit 13
#define ERR_SIZE 11
//Debouncing
#define release 1
#define debounce 2
#define stillPressed 3
#define debounceRelease 4
//Program modes
#define program1 0
#define program2 1
#define program3 2
#define preheat 3
#define ready 4
#define reflow 5
#define cooldown 6
#define done 7
#define abort 8
#define usedefault 9
void intialize();
void keyScan();
void buttonHandle();
void heat();
void pid();
eeprom int tempinput[max_time];
int timeinput, temp,timer,prevtemp=0;
char numinputs;
int err[ERR_SIZE];
char lcdmap[map_size];
int time1, time2, time3;
unsigned char key, butnum, maybe, scanState; //Non-debounced key press
int mode, prevmode;
char digits[10], index, str[32];
unsigned int number = 0;
#include "flash.c"
#include "lcd.c"
//===============================================
//timer 0 compare ISR
interrupt [TIM0_COMP] void timer0_compare(void)
{
//Decrement the three times if they are not already zero
if (time1>0) --time1;
if ((time2>0) && (mode==preheat || mode==ready ||mode==reflow||mode==abort||mode==cooldown))
--time2;
}
//===============================================
void interpolate(void)
{
int i=1,j,k=0;
int lastN=0;
float grad;
while(i<max_time)
{
if(tempinput[i] != 0)
{
grad = ((int)(tempinput[i]-tempinput[lastN]))/(((float)i-(float)lastN));
for(j=lastN+1,k=1; j<i ; j++,k++) tempinput[j] = (k)*grad + tempinput[lastN];
lastN = i;
}
i++;
}
}
//===============================================
int main (void)
{
intialize();
while(1)
{
if(time1 <= 0) keyScan();
if(time2 <= 0) heat();
}
}
//===============================================
void intialize()
{
int i=0, j=0;
for(i=0;i<map_size;i++) lcdmap[i]=0;
for(i=0;i<max_time;i++) tempinput[i]=0;
clear();
pixelxy(10,13,1); pixelxy(20,13,1); pixelxy(30,13,1); pixelxy(40,13,1);
pixelxy(51,34,1); pixelxy(51,54,1); pixelxy(51,74,1); pixelxy(51,94,1); pixelxy(51,114,1);
drawline(0,14,49,14);
drawline(50,14,50,127);
//Temperature labels
sprintf(str,"200"); putstr(8,0,str);
sprintf(str,"150"); putstr(18,0,str);
sprintf(str,"100"); putstr(28,0,str);
sprintf(str," 50"); putstr(38,0,str);
//Time labels
sprintf(str,"60"); putstr(53,30,str);
sprintf(str,"120"); putstr(53,48,str);
sprintf(str,"180"); putstr(53,68,str);
sprintf(str,"240"); putstr(53,88,str);
sprintf(str,"300"); putstr(53,108,str);
//default values
tempinput[0]=90; //Or room temp
tempinput[90]=150;
tempinput[180]=180;
//tempinput[210]=225;
tempinput[240]=225;
tempinput[270]=225;
timeinput=270;
numinputs=5;
interpolate();
scanState = release;
time1 = t1;
time2 = t2;
time3 = t3;
mode=usedefault;
sprintf(str,"Y:USE DEFAULT CURVE N:PROGRAM");
message(str);
for(i = 0; i < 10; i++) digits[i] = 0;
index = 0;
//set up timer 0
TIMSK = 2; //turn on timer 0 cmp match ISR
OCR0 = 250; //set the compare re to 250 time ticks
//prescalar to 64 and turn on clear-on-match
TCCR0=0b00001011;
DDRA = 0x00; //PORTA input
//adc stuff
ADMUX = 0b01100000;
//enable ADC and set prescaler to 1/128*16MHz=125,000
//and clear interupt enable
//and start a conversion
ADCSR = 0b11000111;
//crank up the ISRs
#asm
sei
#endasm
}
//===============================================
//Task subroutines
//keyScan: scan the key
void keyScan()
{
//Reset timeout counter
time1=t1;
//get lower nibble
DDRC = 0x0f;
PORTC = 0xf0;
delay_us(5);
key = PINC;
//get upper nibble
DDRC = 0xf0;
PORTC = 0x0f;
delay_us(5);
key = key | PINC;
//find matching keycode in keytbl
if (key != 0xff)
{
for (butnum=0; butnum<maxkeys; butnum++)
{
if (keytbl[butnum]==key) break;
}
if (butnum==maxkeys) butnum=0;
else butnum++; //adjust by one to make range 1-16
}
else butnum=0;
//debouncing finite state machine
switch(scanState)
{
case release:
if(0x00==butnum)
scanState=release;
else
{
scanState=debounce;
maybe=butnum;
}
break;
case debounce:
if(maybe==butnum)
{
scanState=stillPressed;
buttonHandle();
}
else
scanState=release;
break;
case stillPressed:
if(butnum==maybe)
scanState=stillPressed;
else
scanState=debounceRelease;
break;
case debounceRelease:
if(butnum==maybe)
scanState=stillPressed;
else
scanState=release;
break;
}
}
//===============================================
void buttonHandle()
{
int i;
if((butnum<=10) && (index<10))
{
digits[index++] = butnum - 1 + '0';
digits[index] = NULL;
number=atoi(digits);
if(mode == program1) sprintf(str,"ENTER TIME %d:%d",numinputs,number);
if(mode == program2) sprintf(str,"ENTER TEMPERATURE %d:%dC",numinputs,number);
message(str);
}
if(butnum == no)
{
for(i = 0; i < 10; i++) digits[i] = 0;
number=atoi(digits);
index = 0;
if(mode == 9/*usedefault*/)
{
//PORTA=0x00;
for(i=0;i<max_time;i++) tempinput[i]=0;
timeinput=0;
numinputs=0;
sprintf(str,"ENTER TEMPERATURE:");
mode = program2;
}
else if(mode == program1) sprintf(str,"ENTER TIME %d:%d",numinputs,number);
else if(mode == program2) sprintf(str,"ENTER TEMPERATURE %d:%dC",numinputs,number);
else if(mode == program3)
{
sprintf(str,"PROGRAMMED CURVE:PREHEATING...%dC",temp);
mode = preheat;
}
message(str);
}
if(butnum == yes)
{
if(mode==usedefault)
{
//timeinput=300;
numinputs=6;
drawgraph();
sprintf(str,"DEFAULT CURVE:PREHEATING...%dC",temp);
message(str);
mode = preheat;
}
else if(mode==program1)
{
if(number <= timeinput){
for(i = 0; i < 10; i++) digits[i] = 0;
index = 0;
sprintf(str,"ERROR:MUST BE MORE THAN %d!",timeinput);
message(str);
}
else if(number > max_time){
for(i = 0; i < 10; i++) digits[i] = 0;
index = 0;
sprintf(str,"ERROR:MUST BE LESS THAN %3d!",max_time);
message(str);
}
else{
timeinput = number;
mode = program2;
for(i = 0; i < 10; i++) digits[i] = 0;
number=atoi(digits);
index = 0;
sprintf(str,"ENTER TEMPERATURE %d:", numinputs);
message(str);
}
}
else if(mode==program2)
{
if(number > 250){
for(i = 0; i < 10; i++) digits[i] = 0;
index = 0;
sprintf(str,"ERROR:MUST BE 250C OR LESS!");
message(str);
}
else{
tempinput[timeinput] = number;
mode = program3;
numinputs++;
interpolate();
drawgraph();
sprintf(str,"Y:ADD NEXT POINT N:NO MORE",timeinput,number);
message(str);
}
}
else if(mode==program3)
{
mode = program1;
for(i = 0; i < 10; i++) digits[i] = 0;
number=atoi(digits);
index = 0;
sprintf(str,"ENTER TIME %d:", numinputs);
message(str);
}
else if(mode==ready)
{
timer=0;
ICR1H = 0xf4;
ICR1L = 0x24;
DDRD = 0xff; //PORTD output
TCCR1A = 0b10001110;
TCCR1B = 0b00011100;
OCR1A = 0x0000;
mode=reflow;
}
else if(mode==done)
{
intialize();
}
}
if(butnum==quit)
{
//PORTD.7^=1;
OCR1A = 0;
mode=abort;
sprintf(str,"ABORTING...");
message(str);
}
}
//===============================================
void heat()
{
int adch, adcl;
adcl = ADCL; //Read ADCL first; causes ADC block
adch = ADCH; //Read ADCH; remove the ADC block
adch = adch<<2; //Bits 9:2
adcl = adcl>>6; //Bits 1:0
adch |= adcl; //Index for conversion table
time2 = t2;
prevtemp = temp;
temp = temperature[adch];
ADCSR.6=1;
timer++;
if(mode == preheat){
if (temp < tempinput[0]){
PORTD.5=1;//PORTA = 0x00;// heater on
sprintf(str,"PREHEATING...WAIT:%d C",temp);
message(str);
}
else {
PORTD.5=0;
mode = ready;
cleargraph();
sprintf(str,"READY. INSERT PART AND PRESS Y");
message(str);
}
}
else if(mode==reflow) {
if(timer==timeinput) {
//heater off
//PORTD.7=0;
OCR1A = 0x0000;
mode=cooldown;
sprintf(str,"COOLING DOWN... TEMP:%3dC",temp);
message(str);
}
else{
pid();
//OCR1A = 0x0000;
//if(temp < tempinput[timer])PORTD.5=1;
//else PORTD.5=0;
sprintf(str,"TIME:%3d TMP:%3dC CRV-TMP:%3dC",timer,temp,tempinput[timer]);
message(str);
setcurvepixel(temp,timer);
}
}
else if(mode==cooldown) {
if(temp<=room_temp) {
mode=done;
sprintf(str,"DONE COOLING.REMOVE PART-PRESS Y");
}
else sprintf(str,"COOLING DOWN... TEMP:%3dC",temp);
message(str);
}
else if(mode==abort){
//PORTD.7=0;
// OCR1A = 0x0000;
mode=cooldown;
}
}
void pid()
{
long Kp = 12500; //6250; //Proportional constant
long Kd = 5000;//5000; //Derivative constant
long Ki = 0; //Integral constant
long Kf = 2000; //Future integral error;
long proportional, derivative, integral, futureintegral;
long dutycycle;
char i;
//Keep record of past 10 errors
for(i = ERR_SIZE-1; i > 0; i--){
err[i] = err[i-1];
}
//Error now
err[0] = tempinput[timer] - temp;
proportional = err[0];
derivative = err[0] - err[1];
//Past 10 errors
//integral = 0;
//for(i = 1; i < ERR_SIZE; i++) integral += err[i];
//Look into 10 future errors
futureintegral = 0;
if(timer < (max_time-ERR_SIZE))
//for(i = 1; i < ERR_SIZE*2; i++) futureintegral += tempinput[timer+i] - (temp+i*(temp-prevtemp);
for(i = 1; i < ERR_SIZE; i++) futureintegral += (tempinput[timer+i] - (temp+i*(temp-prevtemp)))
* (ERR_SIZE-i)/(ERR_SIZE);
dutycycle = Kp * proportional + Kd * derivative + Ki * integral + Kf * futureintegral;
if(dutycycle > 62500) dutycycle = 62500;
if(dutycycle < 0 || timer >= timeinput) dutycycle = 0;
OCR1A = dutycycle;
}
flash.c
flash unsigned char smallbitmap[42][4]={
//0
0b00000000,
0b00011111,
0b00010001,
0b00011111,
//1
0b00000000,
0b00000000,
0b00011111,
0b00000000,
//2
0b00000000,
0b00011101,
0b00010101,
0b00010111,
//3
0b00000000,
0b00010101,
0b00010101,
0b00011111,
//4
0b00000000,
0b00000111,
0b00000100,
0b00011111,
//5
0b00000000,
0b00010111,
0b00010101,
0b00011101,
//6
0b00000000,
0b00011111,
0b00010100,
0b00011100,
//7
0b00000000,
0b00000001,
0b00000001,
0b00011111,
//8
0b00000000,
0b00011111,
0b00010101,
0b00011111,
//9
0b00000000,
0b00000111,
0b00000101,
0b00011111,
//:
0b00000000,
0b00000000,
0b00001010,
0b00000000,
//-
0b00000000,
0b00000100,
0b00000100,
0b00000100,
//!
0b00000000,
0b00000000,
0b00010111,
0b00000000,
//.
0b00000000,
0b00000000,
0b00010000,
0b00000000,
//,
0b00000000,
0b00000000,
0b00011000,
0b00000000,
//space
0b00000000,
0b00000000,
0b00000000,
0b00000000,
//A
0b00000000,
0b00011111,
0b00000101,
0b00011111,
//B
0b00000000,
0b00011111,
0b00010101,
0b00001010,
//C
0b00000000,
0b00001110,
0b00010001,
0b00010001,
//D
0b00000000,
0b00011111,
0b00010001,
0b00001110,
//E
0b00000000,
0b00011111,
0b00010101,
0b00010101,
//F
0b00000000,
0b00011111,
0b00000101,
0b00000101,
//G
0b00000000,
0b00001110,
0b00010001,
0b00011101,
//H
0b00000000,
0b00011111,
0b00000100,
0b00011111,
//I
0b00000000,
0b00010001,
0b00011111,
0b00010001,
//J
0b00000000,
0b00010000,
0b00010001,
0b00001111,
//K
0b00000000,
0b00011111,
0b00000100,
0b00011011,
//L
0b00000000,
0b00011111,
0b00010000,
0b00010000,
//M
0b00000000,
0b00011111,
0b00000010,
0b00011111,
//N
0b00000000,
0b00011111,
0b00000001,
0b00011110,
//O
0b00000000,
0b00011111,
0b00010001,
0b00011111,
//P
0b00000000,
0b00011111,
0b00000101,
0b00000111,
//Q
0b00000000,
0b00000111,
0b00000101,
0b00011111,
//R
0b00000000,
0b00011111,
0b00000101,
0b00011011,
//S
0b00000000,
0b00010111,
0b00010101,
0b00011101,
//T
0b00000000,
0b00000001,
0b00011111,
0b00000001,
//U
0b00000000,
0b00011111,
0b00010000,
0b00011111,
//V
0b00000000,
0b00001111,
0b00010000,
0b00001111,
//W
0b00000000,
0b00011111,
0b00001000,
0b00011111,
//X
0b00000000,
0b00011011,
0b00000100,
0b00011011,
//Y
0b00000000,
0b00000011,
0b00011100,
0b00000011,
//Z
0b00000000,
0b00011001,
0b00010101,
0b00010011
};
flash int temperature[1024] = {
272, 271, 270, 269,
267, 266, 265, 264,
263, 262, 261, 260,
259, 258, 257, 256,
255, 254, 253, 252,
251, 250, 249, 248,
247, 246, 245, 244,
243, 242, 241, 240,
239, 238, 238, 237,
236, 235, 234, 233,
232, 231, 231, 230,
229, 228, 227, 227,
226, 225, 224, 223,
223, 222, 221, 220,
220, 219, 218, 217,
217, 216, 215, 215,
214, 213, 212, 212,
211, 210, 210, 209,
208, 208, 207, 206,
206, 205, 205, 204,
203, 203, 202, 202,
201, 200, 200, 199,
199, 198, 197, 197,
196, 196, 195, 195,
194, 194, 193, 193,
192, 191, 191, 190,
190, 189, 189, 188,
188, 187, 187, 186,
186, 186, 185, 185,
184, 184, 183, 183,
182, 182, 181, 181,
181, 180, 180, 179,
179, 178, 178, 178,
177, 177, 176, 176,
176, 175, 175, 174,
174, 174, 173, 173,
172, 172, 172, 171,
171, 171, 170, 170,
170, 169, 169, 169,
168, 168, 168, 167,
167, 167, 166, 166,
166, 165, 165, 165,
164, 164, 164, 163,
163, 163, 162, 162,
162, 162, 161, 161,
161, 160, 160, 160,
160, 159, 159, 159,
158, 158, 158, 158,
157, 157, 157, 157,
156, 156, 156, 156,
155, 155, 155, 155,
154, 154, 154, 154,
153, 153, 153, 153,
152, 152, 152, 152,
151, 151, 151, 151,
150, 150, 150, 150,
150, 149, 149, 149,
149, 148, 148, 148,
148, 148, 147, 147,
147, 147, 147, 146,
146, 146, 146, 146,
145, 145, 145, 145,
145, 144, 144, 144,
144, 144, 143, 143,
143, 143, 143, 142,
142, 142, 142, 142,
141, 141, 141, 141,
141, 140, 140, 140,
140, 140, 140, 139,
139, 139, 139, 139,
138, 138, 138, 138,
138, 138, 137, 137,
137, 137, 137, 136,
136, 136, 136, 136,
136, 135, 135, 135,
135, 135, 135, 134,
134, 134, 134, 134,
133, 133, 133, 133,
133, 133, 132, 132,
132, 132, 132, 132,
131, 131, 131, 131,
131, 131, 130, 130,
130, 130, 130, 130,
129, 129, 129, 129,
129, 129, 128, 128,
128, 128, 128, 127,
127, 127, 127, 127,
127, 126, 126, 126,
126, 126, 126, 125,
125, 125, 125, 125,
125, 124, 124, 124,
124, 124, 124, 123,
123, 123, 123, 123,
123, 122, 122, 122,
122, 122, 122, 121,
121, 121, 121, 121,
121, 120, 120, 120,
120, 120, 120, 119,
119, 119, 119, 119,
119, 118, 118, 118,
118, 118, 117, 117,
117, 117, 117, 117,
116, 116, 116, 116,
116, 116, 115, 115,
115, 115, 115, 115,
114, 114, 114, 114,
114, 114, 113, 113,
113, 113, 113, 113,
112, 112, 112, 112,
112, 112, 111, 111,
111, 111, 111, 110,
110, 110, 110, 110,
110, 109, 109, 109,
109, 109, 109, 108,
108, 108, 108, 108,
108, 107, 107, 107,
107, 107, 107, 106,
106, 106, 106, 106,
106, 105, 105, 105,
105, 105, 105, 104,
104, 104, 104, 104,
104, 103, 103, 103,
103, 103, 103, 102,
102, 102, 102, 102,
102, 101, 101, 101,
101, 101, 101, 100,
100, 100, 100, 100,
100, 99, 99, 99,
99, 99, 99, 98,
98, 98, 98, 98,
98, 97, 97, 97,
97, 97, 97, 96,
96, 96, 96, 96,
96, 96, 95, 95,
95, 95, 95, 95,
94, 94, 94, 94,
94, 94, 93, 93,
93, 93, 93, 93,
93, 92, 92, 92,
92, 92, 92, 92,
91, 91, 91, 91,
91, 91, 90, 90,
90, 90, 90, 90,
90, 89, 89, 89,
89, 89, 89, 89,
88, 88, 88, 88,
88, 88, 88, 87,
87, 87, 87, 87,
87, 87, 86, 86,
86, 86, 86, 86,
86, 86, 85, 85,
85, 85, 85, 85,
85, 84, 84, 84,
84, 84, 84, 84,
84, 83, 83, 83,
83, 83, 83, 83,
83, 82, 82, 82,
82, 82, 82, 82,
82, 81, 81, 81,
81, 81, 81, 81,
81, 81, 80, 80,
80, 80, 80, 80,
80, 80, 80, 79,
79, 79, 79, 79,
79, 79, 79, 79,
78, 78, 78, 78,
78, 78, 78, 78,
78, 77, 77, 77,
77, 77, 77, 77,
77, 77, 77, 76,
76, 76, 76, 76,
76, 76, 76, 76,
76, 75, 75, 75,
75, 75, 75, 75,
75, 75, 75, 74,
74, 74, 74, 74,
74, 74, 74, 74,
74, 74, 73, 73,
73, 73, 73, 73,
73, 73, 73, 73,
73, 72, 72, 72,
72, 72, 72, 72,
72, 72, 72, 72,
71, 71, 71, 71,
71, 71, 71, 71,
71, 71, 71, 70,
70, 70, 70, 70,
70, 70, 70, 70,
70, 70, 69, 69,
69, 69, 69, 69,
69, 69, 69, 69,
69, 68, 68, 68,
68, 68, 68, 68,
68, 68, 68, 67,
67, 67, 67, 67,
67, 67, 67, 67,
67, 66, 66, 66,
66, 66, 66, 66,
66, 66, 66, 65,
65, 65, 65, 65,
65, 65, 65, 65,
64, 64, 64, 64,
64, 64, 64, 64,
63, 63, 63, 63,
63, 63, 63, 63,
62, 62, 62, 62,
62, 62, 62, 62,
61, 61, 61, 61,
61, 61, 61, 60,
60, 60, 60, 60,
60, 59, 59, 59,
59, 59, 59, 58,
58, 58, 58, 58,
58, 57, 57, 57,
57, 57, 57, 56,
56, 56, 56, 56,
55, 55, 55, 55,
55, 54, 54, 54,
54, 53, 53, 53,
53, 53, 52, 52,
52, 52, 51, 51,
51, 51, 50, 50,
50, 50, 49, 49,
49, 49, 48, 48,
48, 47, 47, 47,
47, 46, 46, 46,
45, 45, 45, 44,
44, 44, 43, 43,
43, 42, 42, 42,
41, 41, 41, 40,
40, 40, 39, 39,
39, 38, 38, 37,
37, 37, 36, 36,
35, 35, 35, 34,
34, 33, 33, 32,
32, 31, 31, 31,
30, 30, 29, 29,
28, 28, 27, 27,
26, 26, 25, 25,
24, 24, 23, 23,
22, 21, 21, 20,
20, 19, 19, 18,
17, 17, 16, 16,
15, 14, 14, 13,
13, 12, 11, 11,
10, 9, 9, 8,
7, 7, 6, 5,
4, 4, 3, 2,
1, 1, 0, -1,
-2, -2, -3, -4,
-5, -5, -6, -7,
-8, -9, -10, -10,
-11, -12, -13, -14,
-15, -16, -17, -18,
-18, -19, -20, -21,
-22, -23, -24, -25
};
flash unsigned char keytbl[maxkeys]={ 0x7d,
0xee, 0xed, 0xeb,
0xde, 0xdd, 0xdb,
0xbe, 0xbd, 0xbb,
0x7e, 0x7b,0xe7};
lcd.c
/*******************************************************************************************************
LCD Signals according to the datasheet
Signal Description Pin HIGH/LOW
DB Databus 4-11 (high)
CS1 Select Column 1 - 63 12 (low)
CS2 Select Column 64-127 13 (low)
RS Reset 14 (low)
R/W Read / Write 15 (read/write)
D/I Data / Instruction 16 (data/instruction)
E Enable 17 (H)
*******************************************************************************************************/
// "SET" _always_ means HIGH = 5v as you would measure with a scope
// "CLR" _always_ means LOW = 0v as you would measure with a scope
// R/W Read / Write 15 (read/write)
#define Set_RW (PORTD |= 0x08)
#define Clr_RW (PORTD &= ~0x08)
// D/I Data / Instruction 16 (data/instruction)
#define Set_DI (PORTD |= 0x10)
#define Clr_DI (PORTD &= ~0x10)
// E Enable 17 (H)
#define Set_E (PORTD |= 0x20)
#define Clr_E (PORTD &= ~0x20)
// CS1 Select Column 1 - 64 12 (low)
#define Set_CS1 (PORTD |= 0x01)
#define Clr_CS1 (PORTD &= ~0x01)
// CS2 Select Column 65-128 13 (low)
#define Set_CS2 (PORTD |= 0x02)
#define Clr_CS2 (PORTD &= ~0x02)
// RS Reset 14 (low)
#define Set_RS (PORTD |= 0x04) // note: Active Low! switched logic
#define Clr_RS (PORTD &= ~0x04)
#define data_out(x) (PORTB = x)
//===============================================
char getval(int x, int y)
{
signed char row;
row=x/8;
return lcdmap[8*y + row];
}
//===============================================
void updateval(int x, int y, signed char val)
{
signed char row;
row=x/8;
lcdmap[8*y + row]=val;
}
//===============================================
void putbyte(int page, int address, char val)
{
if(address<64)
{
Clr_CS1;
Set_CS2;
delay_us(1);
}
else
{
Set_CS1;
Clr_CS2;
delay_us(1);
}
//Set X address
PORTB = page|0xB8;
delay_us(1);
Set_E;
delay_us(1);
Clr_E;
delay_us(5);
//delay_ms(1);
//Set Y address 0
PORTB = address|0x40;
delay_us(1);
Set_E;
delay_us(1);
Clr_E;
delay_us(5);
//delay_ms(1);
//Aim at the data register.
Set_DI;
delay_us(1);
PORTB = val;
updateval(8*page,address,val);
delay_us(1);
Set_E;
delay_us(1);
Clr_E;
delay_us(5);
//delay_ms(1);
Clr_CS1;
Clr_CS2;
//Aim back to the control register.
Clr_DI;
delay_us(1);
}
//===============================================
void clear(void)
{
char col, row;
DDRD = 0xFF;
DDRB = 0xFF;
//Idle E
Clr_E;
// Make sure we're writing.
Clr_RW;
//Reset the LCD controllers
Clr_RS;
delay_us(5);
//delay_ms(100);
Set_RS; // Not resetting.
delay_us(5);
//delay_ms(100);
// Talk to control register
Clr_DI;
// Talk to both controllers
Clr_CS1;
Clr_CS2;
// Display On
PORTB = 0x3F;
delay_us(1);
Set_E;
delay_us(1);
Clr_E;
delay_us(5);
//delay_ms(10);
// Display Start Line: AAAAA : RW/DI/DB7:DB0 "0/0/11AAAAAA"
PORTB = 0xC0;
delay_us(1);
Set_E;
delay_us(1);
Clr_E;
delay_us(5);
//delay_ms(10);
for(row=0;row<=7;row++)
{
//Set X address
PORTB = 0xB8|row;
delay_us(1);
Set_E;
delay_us(1);
Clr_E;
delay_us(5);
//delay_ms(1);
//Set Y address 0
PORTB = 0x40;
delay_us(1);
Set_E;
delay_us(1);
Clr_E;
delay_us(5);
//delay_ms(1);
//Aim at the data register.
Set_DI;
delay_us(1);
//Talk to controller 1 only
Set_CS1;
Clr_CS2;
delay_us(1);
for(col=0;col<=63;col++)
{
//FDATA(cfag12864b[row][col]);
PORTB = 0x00;// col;
delay_us(1);
Set_E;
delay_us(1);
Clr_E;
delay_us(5);
//elay_ms(1);
}
//Talk to the controller 2
Clr_CS1;
Set_CS2;
delay_us(1);
for(col=64;col<=127;col++)
{
//FDATA(cfag12864b[row][col]);
PORTB = 0x00;//col;
delay_us(1);
Set_E;
delay_us(1);
Clr_E;
delay_us(5);
//delay_ms(1);
}
//Talk to both controllers
Clr_CS1;
Clr_CS2;
//Aim back to the control register.
Clr_DI;
delay_us(1);
} // end of column loop
}
//===============================================
void pixelxy(signed char x, signed char y, signed char on)
{
signed char col, row, val;
if(x<0 || x>63) return;
if(y<0 || y>127) return;
DDRD = 0xFF;
DDRB = 0xFF;
col = y%64;
row = x/8;
val = getval(x,y);
//val = val | (1<<(x%8));
if (on != 0) val = val | (1<<(x%8));
else val = val & ~(1<<(x%8));
if(y<64)
{
Clr_CS1;
Set_CS2;
delay_us(1);
}
else
{
Set_CS1;
Clr_CS2;
delay_us(1);
}
PORTB = 0xB8|row;
delay_us(1);
Set_E;
delay_us(1);
Clr_E;
delay_us(5);
//delay_ms(1);
//Set Y address 0
PORTB = (col)|0x40;
delay_us(1);
Set_E;
delay_us(1);
Clr_E;
delay_us(5);
//delay_ms(1);
//Aim at the data register.
Set_DI;
delay_us(1);
PORTB = val;
updateval(x,y,val);
delay_us(1);
Set_E;
delay_us(1);
Clr_E;
delay_us(5);
//delay_ms(1);
/*Clr_CS1;
Set_CS2;
delay_us(1);*/
Clr_CS1;
Clr_CS2;
//Aim back to the control register.
Clr_DI;
delay_us(1);
}
//===============================================
void drawline(char x1, char y1, char x2, char y2)
{
int e;
int j;
signed char dx,dy,/*j,*/ temp;
signed char s1,s2, xchange;
signed char x,y;
x = x1;
y = y1;
dx = cabs(x2-x1);
dy = cabs(y2-y1);
s1 = csign(x2-x1);
s2 = csign(y2-y1);
xchange = 0;
if (dy>dx)
begin
temp = dx;
dx = dy;
dy = temp;
xchange = 1;
end
e = ((int)dy<<1) - dx;
for (j=0; j<=dx; j++)
begin
pixelxy(x,y,1) ;
if (e>=0)
begin
if (xchange==1) x = x + s1;
else y = y + s2;
e = e - ((int)dx<<1);
end
if (xchange==1) y = y + s2;
else x = x + s1;
e = e + ((int)dy<<1);
end
}
//===============================================
void putchars(char x, char y, char letter)
{
char i, j;
char col, row, val, index, mask;
col = y%64;
row = x/8;
if (letter>='0' && letter<=':') index = letter-'0';
else if (letter == '-') index = 11;
else if (letter == '!') index = 12;
else if (letter == '.') index = 13;
else if (letter == ',') index = 14;
else if (letter == ' ') index = 15;
else index = letter-'A'+16;
mask = 0b00011111<<(x%8);
for(i=0; i<4; i++)
{
val = getval(x,y+i);
val = val & ~mask; //Clear the rows in which the alphabets go
val = val | smallbitmap[index][i]<<(x%8);
putbyte(x/8,y+i,val);
}
if((x%8)>3)
{
mask = (0xff<<((x%8)-3));
for(i=0; i<4; i++)
{
val = getval(x+8,y+i);
val = val & mask; //Clear the rows in which the alphabets go
val = val | smallbitmap[index][i]>>(8-(x%8));
putbyte(x/8+1,y+i,val);
}
}
}
//===============================================
void putstr(char x, char y, char *string)
{
char i;
i = 0;
while(string[i] != NULL)
{
putchars(x, y+i*4, string[i]);
i++;
}
}
//===============================================
void message(char *string)
{
char i;
for(i = strlen(string); i<32; i++)
string[i] = ' ';
for(i = 0; i < 32; i++)
putchars(59, i*4, string[i]);
}
//==============================================
void drawgraph(void)
{
int i;
int x,y;
for(i=0; i<max_time; i++)
{
x = 50-((tempinput[i]*49)/250);
y = (100*(i)/300)+14;
pixelxy((char)x,(char)y,1);
//delay_ms(1);
}
}
Appendix B: Schematics
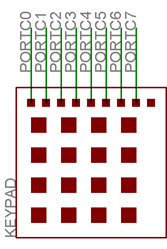
Figure 8: Keypad schematic
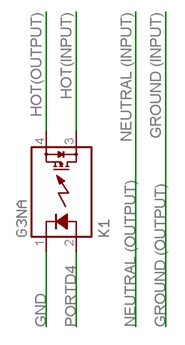
Figure 9: Relay box schematic
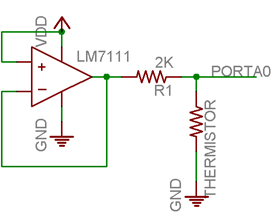
Figure 10: Thermistor schematic
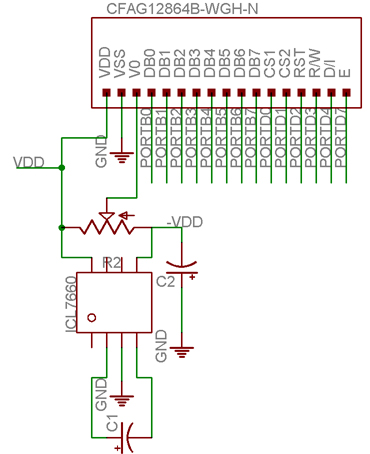
Figure 11: LCD schematic
Appendix C: Parts List
Item Cost
Omron solid state relay Free sample
Maxim ICL7660CPA Free sample
Used toaster oven Free
LM7111 op-amp In lab
Potentiometer In lab
Crystal oscillators In lab
Resistors and capacitors In lab
Solder board $2.50
Power supply $5.00
Custom PC board $5.00
Keypad $6.00
Atmel Mega32 $8.00
Crystalfontz CFAG12864-WGH-N $18.09
AC receptacle connector $0.64
3AG fuse holder $0.75
NTC thermistor x2 $0.98
Relay box hardware $5.82
TOTAL $52.78
Table 5: Parts list
Appendix D: Tasks
Ko Ihara's tasks:
- Parts research, and sample requests
- Relay box construction
- Protoboard construction
- Various machining tasks
- Basic LCD pixel manipulation programming
- Control algorithm programming
Kashif Javed's tasks:
- Parts resarch
- Printed circuit board component population
- LCD graphical functions programming
- Line interpolation programming
- Control algorithm programming
Appendix E: References
Sample Sponsors:
Datasheets:
- Atmel Mega32
- BC 2322 633 83303 NTC Thermistor
- Crystalfontz CFAG12864B-WGH-N
- LM7111 Operational Amplifier
- Maxim ICL7660CPA Reverse Voltage Generator
- Omron G3NA Solid State Relay
Vendor Sites:
Pictures
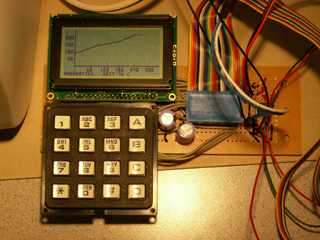
Figure 12: LCD board with target profile drawn
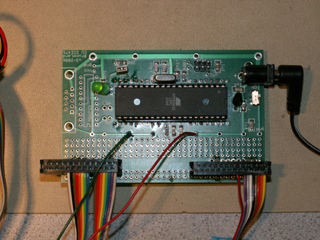
Figure 13: MEGA32 board
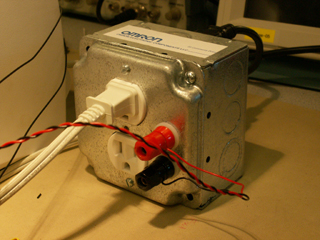
Figure 14: Relay box (front)

Figure 15: Relay box (back)
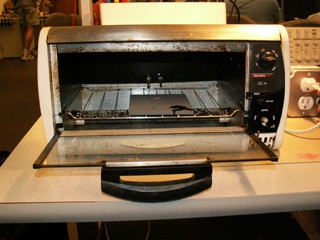
Figure 16: Hacked toaster oven with thermistor
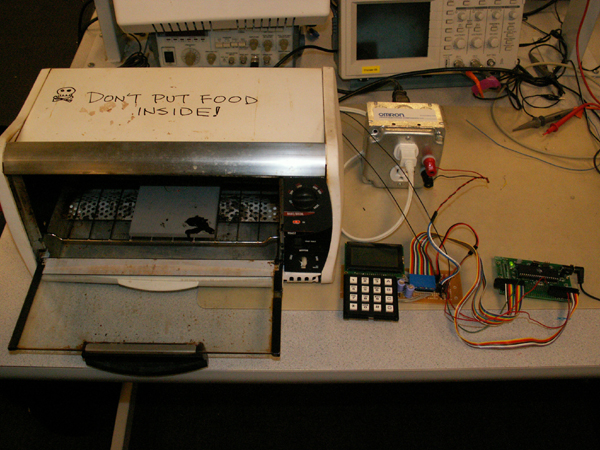
Figure 17: Complete system picture
Acknowledgements
We would like to thank Omron Electronics and Maxim IC for their generous parts samples.
We would also like to acknowledge Professor Bruce Land for providing us with various
harnesses and connectors.