Prototype
Once the functional requirements of the
board was identified (see overview),
hardware schematics were drafted. The initial design
consisted of 3 functional circuits, which are very close to
the boards used on the existing PCB.
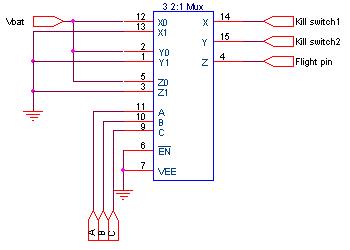
The circuit that simulates the the
kill switch and flight pin is shown above. The design of
this circuit is very straightforward: Power Board Connector
B has GND, VBatt and select lines on it. When the Flight Pin
select line is connected to VBatt and either one or both of
the kill switches are connected to VBatt, the satellite will
turn on. Since the select lines are inputs to Mosfet gates
on the power board, there is little to no current draw and
the use of the Multiplexer as shown in the above schematic
makes sense.
However, we did run into some
voltage issues: The DIP package of the multiplexer that we
used works correctly when sending 12V through it, while the
SMT component will flake out, usually permanently at larger
voltages. This caused severe inconsistencies during testing
of our prototype and PCB circuitries. Unfortunately, we have
determined this limitation ultimately keeps our maximum MUX
voltages to around 3V for all circuits and prevents us from
sending VBatt (12V) through to demonstrate integrated
functionality of the Power Board and Diagnostics Board. This
demonstration of proper functionality has further
ramifications in other circuits as they too were prototyped
with the DIP package and break in similar ways.
This issue can be easily resolved
with these higher voltage multiplexers. Unfortunately, our
board does not have a compatible pin out with these
components & can therefore should not be hooked up to the
power board directly. Initially, the multiplexer was chosen
because of its availability and cost. Our first choice was a
MAXIM chip that ran off of any voltage between 5 and 36V and
allowed for any value between Vcc+.5 and Vee - .5 to pass.
This part was unavailable at the time and was a bit too
expensive to use in each of the circuits as required.
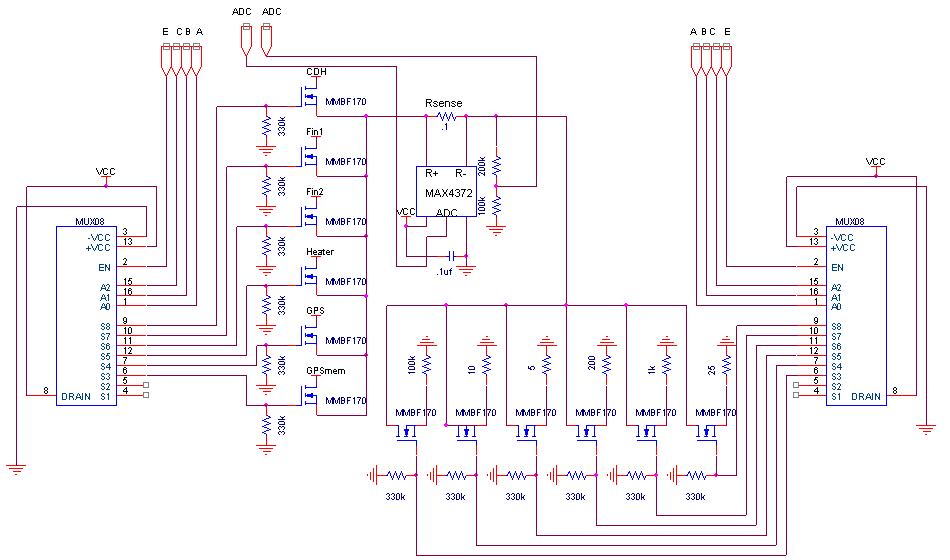
Once the circuit to test "power on"
was created and tested, a regulator measurement circuit was
created (above). The regulator expands in complexity
compared to the Kill Switch & Flight Pin simulation circuit.
This circuit uses 2 8:1 demuxes to allow the Diagnostics
board to select one regulated input, pass the current
through a common RSense resistor and Voltage divider and
finally selecting which of 4 power resistor loads to use.
The first MUX chooses the input to measure. The
demultiplexer has 5V as a single input and 8 outputs that
are connected to the gates of transistors (all of which have
pull downs for when they are not being selected). This
allows us to select which one transistor to turn on. The
transistor that turns on, passes its input voltage from
source to drain. Once through the transistor, the signal
passes through a .1 Ohm sense resistor. A MAX4372 is used to
measure the voltage on either side of the sense resistor,
which then provides the ADC with a voltage that represents
the current based on the knowledge that there was a .1 ohm
resistor there. Once through the sense resistor, a voltage
divider sends 1/3 of the voltage to the MCU to allow it to
take measurements up to about 15V. At this point, another
MUX is controlled by the MCU, which selects the appropriate
power resistor to load the regulator signals with in the
same way the first MUX selected the transistor. This design
ensures that only one of the regulator outputs be loaded at
a time. Additionally, when voltages are being read, the
second mux is disabled to get an accurate voltage reading.
This is consistent with the power test document as well as
the projects goals.
Simply selecting the appropriate
regulator to load is not sufficient as they won't be on by
default. To turn the circuits on, a voltage must be applied
by the MCU to the select line going into the power board
this voltage comes from PORTB.4-7 and PORTC.0-5. In future
revisions, this may be removed due to the active effort to
make the power board control its own hardware and depend on
MCU communications rather than voltage levels, which will
add reliability as well as reduce I/O requirements.
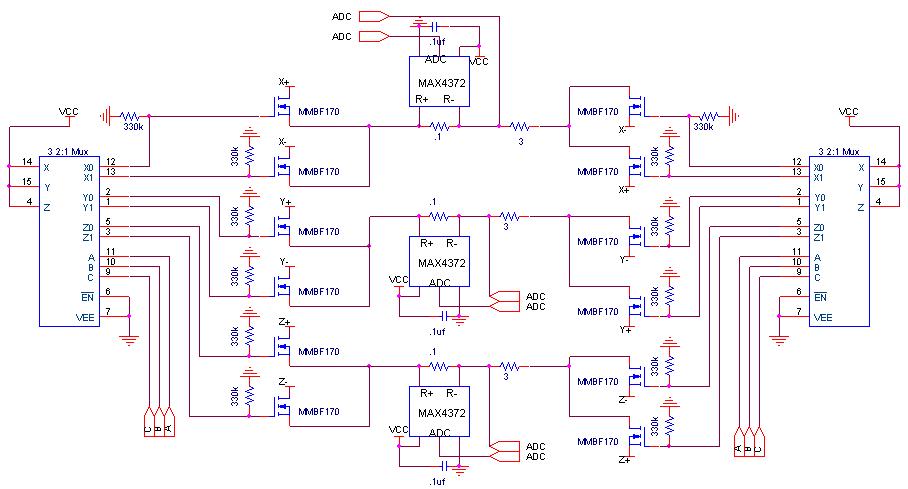
The torque coils test circuit is the
most complicated of the 3 and we were prepared to see issues
with it due to its bidirectional nature. This circuit is
similar to the 8:1 MUX circuit. However, it uses 2:1 MUXes
and is repeated 3 times (once for each axis). The select
lines of the multiplexers are tied together. When a select
line is asserted, one direction for the axis is selected on
one side and the opposite direction is selected on the
other. This effectively reverses the H-bridge bi directional
effect and allow the current sensors to deal with just one
direction of current. Unfortunately, we did not hook the MUX
enable lines up to port pins for this circuit. Doing so
would create a much more accurate Voltage reading as the
last transistor essentially becomes an open circuit and the
voltage divider is much more useful.
There are various capacitors,
resistors, crystals, headers, etc. that connect to the ZIF
socket. If interested in recreating a 128L board, use the
ExpressPCB file for reference. Please see PCB errors in
Schematics.
MEGA128 Port Assignments
PORT Designations:
PORTA = LCD Driver
PORTB = voltage mux(0), select lines(4-7)
PORTC = Coils select lines(0-5), coils mux(6-7)
PORTD = LEDs (0-1), Serial Comm1 (2-3), current mux(4-7)
PORTE = serial Comm0 & Programming (0-1), fpks mux(2-4), voltage mux(5-7)
PORTF = ADCs
PORTG = LED's (0-1), coils mux(2), Not used(3-4)
PCB
Our
project was
laid out by hand in
ExpressPCB. The layout took at least 75 hours combined.
The board is relatively large, especially when compared to
the power board. Fortunately, our careful layout paid off.
Upon population of about 162 components, the MCU immediately
worked, with the exception of a quirky & inconsistent
Serial0 receive issue upon reset. Other errors were found,
but largely the board layout was fine.
PCB Features Include
- The PCB is a 4 layer board
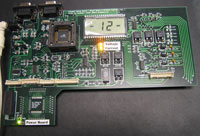
- Middle 2 layers are ground
plane and a +5V rail
- Programming header for use with
STK500
- Successfully runs code on a
Mega 128L @ 8MHz, 5V.
- (2) RS-232 connections
- On / Off switch
- 4 Digit 7-Segment Display w/ 1
Port Driver
- 2 MCU Controllable
Red/Orange/Green LEDs
- 12V Regulator 2A Circuit
Breaker
- 12V Short Status LED.
- ZIF Socket for TQFP64
- 1:1 Power board connectors for
easy diagnostics
MCU Selection
The processor itself supports dual
serial communications and has 7 Ports. Aside from being
free, these are the two main reasons for MCU selection. The
dual serial ports connect to a MAX232 surface mount IC.
Serial0 is accessible through the 9 Pin serial connector
while Serial1 is accessible through either the second port
or the power board MOLEX connector, which is set by a
jumper.
Hardware Design Issues
Once populated, we ran into problems
detecting voltages and current changes above around 3V. This
was quickly found to be a transistor biasing problem. In
order to detect voltage drops, our design requires us to
operate in the triode region through 12V. However, due to
the 3V restriction on Vgs due to the
MUX limitation, we end up saturating
early and the current becomes limited but this more to do
with being on the wrong Vgs curve as opposed to being in the
saturation regime. Since the transistors are not biased
appropriately, they don't behave like an on off switch as
intended, but this should become significantly better with a
higher Vgs. If the same design is kept in the future, the
following inequality must hold true: Vds
< Vgs - Vtn
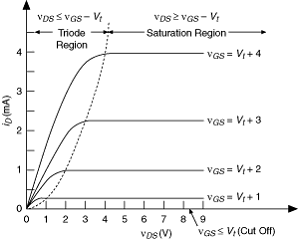
We have a good idea regarding a fix
and many suggestions have been given to us, but they all
require drastic hardware changes. The following are the best
candidates thus far and will be considered for future
revisions.
- Instead of reusing circuit
paths, use one current sensor and voltage divider per
component - then use MUX for MCU ADC signals.
- Use MUX and FET that when
combined can still bias Vgs much higher to keep power
FET in the ohmic regime for all measurements
Another issue is the current is most
likely being limited through the transistor at time, more
testing should be done to correlate the amount of current
drawn by this board, during manual power board testing and
during flight operations.
|