High Level Design
Rationale & Source of
Project Idea
Bryan has been a member of the CubeSat project since
September 2003. The need for this power diagnostic board
became very clear over the last year and half. Since then, there
have been about 5 power board revisions, but the requirements and
testing procedures have remained the same. Qualifying a
single board was a long and tedious process, which was prone
to user error and loose wires and even board malfunction due
to violations of procedure. Additionally, qualification was
generally not done again until a very important test and
often problems were not found until something was obviously
broken, current leaks were found or the board smoked.
After discussions with Professor
Mark Campbell, it was decided that diagnostic & test
hardware would be useful for all boards, especially the
power board since there is an intention to make a new
cubesat in the coming years and it can be adapted to the new
CU Sat project, which is now in its System Concept Review
stage. This board can be easily be expanded for DC tests and
can probably be adapted to qualify continuous AC signals
with some minor modifications.
While this project is a joint effort
between the CubeSat project and ECE 476, it was not
something that Michael or Bryan would have been doing anyway
and was thus acceptable as an ECE476 final project. Had this
initial board not been made, it most likely would have been
given lower priority and likely not have found itself
included in the new spacecraft to be designed.
Background Math
Our ADCs calculate the
incoming voltages using the following equations:
- General Regulator Current
Measurement (8:1 Mux) = (ADCH / 255) * (Aref/Gain) *
Scale
- Aref = 5.022 V; Measured
for this board
- Gain = 50; Due to 50 gain
associated to the current sensor
- Scale = 11; Due to the .1
Ohm Sense Resistor Used
- General Regulator Voltage
Measurement (8:1 Mux) = (ADCH / 255) * (Aref /
VoltageDividerFactor)
- ARef = 5.022V; Measured for
this board
- Voltage Divider Factor = .5
(R1 = R2)
- Coil Current Measurement (8:1
Mux) = (ADCH / 255) * (Aref/Gain) * Scale
- Aref = 5.022 V; Measured
for this board
- Gain = 50; Due to 50 gain
associated to the current sensor
- Scale = 135; Measured Scale
Factor - should be 11
This scale factor is based on experimental
calibration. It is wrong due to transistor voltage
dropoff and causes a somewhat unstable reading. This
will be fixed in a future revision of the board.
- Coil Voltage Measurement (8:1
Mux) = (ADCH / 255) * (Aref / VoltageDividerFactor) + Vds1
+ Vds2
- ARef = 5.022V; Measured for
this board
- Voltage Divider Factor = .5
(R1 = R2)
Logical Structure
The CubeSat power board provides
power to all subsystems in the satellite. In the satellite,
the board is commanded by the Command and Data Handling
Subsytem by toggling select lines. When a subsystem's select
line is pulled high, the power board switches on the supply
for that subsystem. In simple terms, the Diagnostic board
takes the role of commanding the power board and loading the
power board to simulate connected subsystems.
There are 4 voltage levels provided
by the power board: 1.5V, 3.3V, 5V, 12V. The first three
voltages are supplied from a switching regulator while the
final one is the battery voltage (3 lithium ion cells in
series). These supplies are sent to other subsystems, which
can be simulated as power resistors.
For reference, the following is a
crude block diagram represents the main interactions within
our PCB.
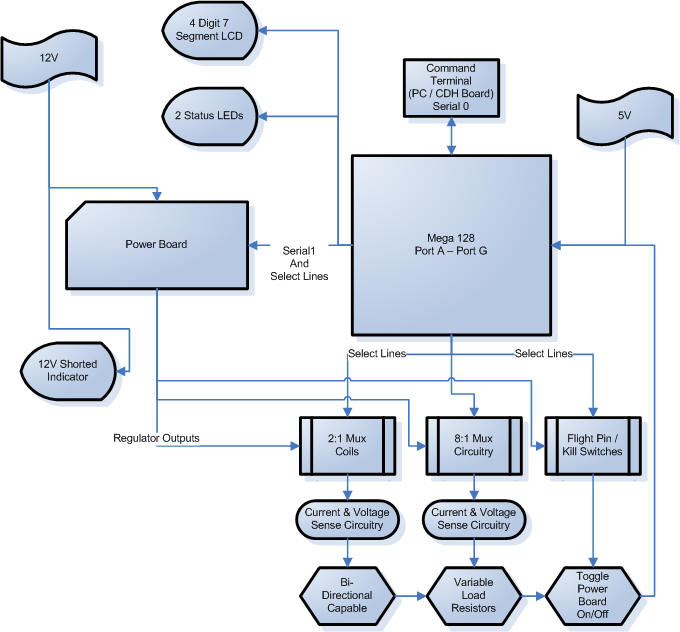
The Diagnostic Board Must:
- Simulate Kill Switches and
Pull Before Flight Pin
The power board is the heart of the
satellite. It must be on for anything else in the
satellite to be on. In order to control when the
satellite is on or off, mechanical switches are used. 2
of the switches are micro switches on top of the
satellite and the 3rd is a micro switch that gets
toggled by a pin that is inserted into the side of the
satellite, which is removed before flight. In order for
the satellite to be on, the following conditions are
met: The Pin is out and at least 1 of the 2 micro
switches are not depressed. When the switch is not
depressed in all 3 cases, a high voltage is sent to the
select lines of the appropriate switch. The following
table represents whether the satellite is on or off.
This is the first step in testing the board as it is the
most basic task and the board must be on for other tests
to function.
Flight Pin |
Kill Switch 1 |
Kill Switch 2 |
Satellite State |
0 |
0 |
0 |
Off |
0 |
0 |
1 |
Off |
0 |
1 |
0 |
Off |
0 |
1 |
1 |
Off |
1 |
0 |
0 |
Off |
1 |
0 |
1 |
On |
1 |
1 |
0 |
On |
1 |
1 |
1 |
On |
- Measure Voltage & Current
for each regulator output on the power board
The power board has 4 regulators
that are sent to the Heaters, CDH, Comm (Vestigial),
GPS, GPS Mem, Boom Burn Wire, and the Flap Burn Wire.
Each of these components have different loads. As a
result, the board must be able to turn on any of these
inputs through the select pins on the power board,
measure the voltage and current for the selected
component and apply the appropriate power resistor. This
recreates the more thorough power board test.
- Measure Voltage & Current
for the bidirectional torque coils
The torque coils on the CubeSat are
used for attitude control. There is one coil on each
axis of the satellite. When current is applied through
the coil, the satellite tries to align itself with the
earth's magnetic field. However, in order to apply
torque in the opposite direction, the current must be
reversed. This bidirectional nature requires a different
circuit from normal regulator measurements. The board
must allow for current to flow in either direction, and
be able to measure both current and voltage.
- Communicate to the Power
Board via Serial Connection
The power board cannot be changed
to accommodate new tests. As a result, a big portion of
the board cannot be tested as we are limited to the pins
available through the well defined connectors. However,
the power board has a serial connection, which has a MCU
connected to various sensors. As a result, this serial
communications can allow for more complex tasks to take
place.
Standards
Due to the highly customized
solution this project applies to, few standards were used.
RS-232 was implemented for communicating between the Mega128
and the Computer terminal & the Mega128 and the Power Board.
For cubesat, since this is an external board, we do not need
to be concerned about materials used with regard to a space
mission. However, the design for CUSat will have to take
into account temperature range (-20C - 70C), Vibration,
Radiation, ESD and must conform to a specific list of
allowable materials.
In a sense, the cubesat interface
itself is a standard which we must follow. As discussed in
our conclusions, aside from our lower than desirable
operating conditions, the board is on track to integrate
with a power board.
Existing patents,
trademarks, copyrights
After a reasonable search for such
items, none were found to conflict with our project. |